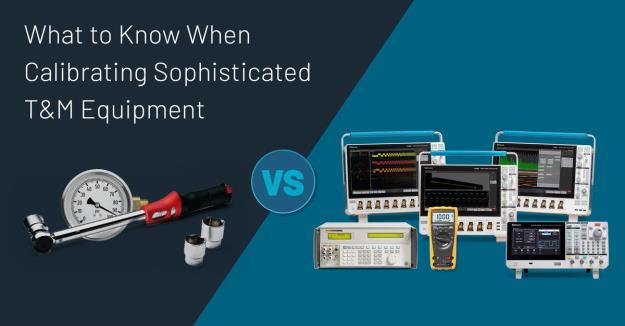
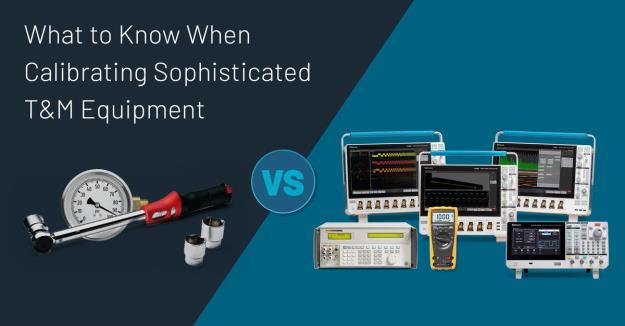
Would you take your Ferrari to the neighborhood mechanic? Probably not. So why would you take your sophisticated electronic test and measurement equipment to a shop that specializes in simple tool calibrations?
Rapid growth in infrastructure technologies like 5G and semiconductors as well as an overall increase in the use of electronic and RF components in consumer products is fueling significant growth in the demand for the sophisticated test and measurement equipment required during the manufacturing process (Markets and Markets, Test and Measurement Equipment Global Forecast, April, 2021). The general purpose test equipment (GPTE) market, which includes oscilloscopes, network analyzers, digital multimeters, and other bench-top equipment, is expected to comprise the largest share of the market through at least 2025.
Maintaining general purpose test and measurement equipment through regular calibration is vital to ensuring accurate, repeatable measurements that give you confidence in your manufacturing processes. Plus, in many of these growing industries, certificated calibration on this equipment is required to satisfy company quality policies and/or external audit requirements such as AS9100 or IATF 16949.
As a leading provider of quality calibration services, we are often asked:
- What are the skills, equipment and qualifications needed to calibrate this high end, increasingly sophisticated test and measurement equipment?
- What equipment should we calibrate in-house?
- What’s the difference between calibrating a sophisticated piece of equipment like a waveform generator or oscilloscope and a less-sophisticated piece of equipment like a gauge block?
Here are four important factors to consider when calibrating high end test and measurement equipment:
Calibration Equipment Requirements
In the simplest of terms, equipment calibration involves comparing measurements from a piece of equipment known to be accurate against the device under test. That means you need an accurate equipment standard on hand for each type of equipment you are calibrating. The equipment required to calibrate less complex instruments like a torque wrench is very inexpensive and easy to use.
However, if you need to calibrate a high-end 50 Ghz spectrum analyzer for example, this requires investment in all the equipment required to fully calibrate that instrument. A test stand for these more sophisticated instruments can cost up to $500k.
Given the cost of procuring and maintain equipment standards, it’s hard for in-house calibration labs or even smaller third-party calibration service providers to secure the required capital and to justify the expense. In fact, a common practice amongst smaller calibration service providers is to claim the ability to calibrate a piece of equipment but then send the equipment to an OEM like Tektronix to perform the calibration. This increases costs and adds to the turnaround time for your calibration.
In another scenario, we often see that because of the cost of the equipment, smaller non-OEM vendors may ship standards between labs or ship your equipment to a lab that has the right standard, adding cost and turnaround time to your calibration.
Smaller, non-OEM calibration vendors are often better suited to completing calibrations for less sophisticated equipment like pressure gauges, torque wrenches, and other physical-dimensional equipment that requires less skill, automation, and calibration equipment.
Like many manufacturers, one prime aerospace contractor struggled to keep up with its equipment maintenance program. The focus on lean manufacturing combined with wide array of sophisticated test and measurement assets made it difficult for them to keep up with the capital investments required. Without in-house capabilities, they were also sending different types of equipment to various service providers which resulted in quality discrepancies as well as long turnaround times.
“Our biggest challenge is probably the lack of capital to build our internal capabilities. We’ve got the expertise, but getting the equipment to do some cals is hard.” – Quality Manager
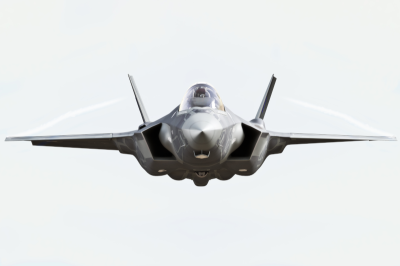
After surveying multiple vendors on accredited calibration capabilities, examining their quality history, and completing an onsite audit, the aerospace company decided to partner with Tektronix to augment their internal calibration lab. They now have a single vendor that can calibrate everything in their lab, including the most sophisticated electronic test and measurement instruments.
Technician Training and Certifications
Trained, certified, and experienced technicians are essential for successfully calibrating sophisticated test equipment, especially if there are multiple brands of equipment such as Rohde & Schwartz, NI, Keysight, or Tektronix. Technicians who have been hands-on for years are familiar with the automated test procedures and are quick to diagnose problems with equipment.
Finding well-qualified technicians can be difficult, so some calibration vendors and in-house labs rely on on-the-job training for technicians and develop internal certification programs.
For high end equipment, we suggest you consider only labs that are accredited by A2LA, where technician training is required as part of the accreditation process. Accredited calibration labs must identify core competencies, document the personnel training, and monitor the technician’s work quality with live skill demonstrations and proficiency testing.
At Tektronix, more than 80% of our technicians have completed the American Society for Quality (ASQ) Certified Calibration Technician (CCT) certification. Tektronix understands the importance of investing in people and pays for its technicians to complete both ASQ and CCT certifications.
Automated Test Sequences
Unlike physical-dimensional calibrations of tools like torque wrenches, calibrations of sophisticated electronic test and measurement equipment including spectrum analyzers, oscilloscopes, and power supplies require a significant level of automation to make repeated measurements while measuring several inputs at the same time. Aside from exceptional accuracy and repeatability, automation has the added benefit of speeding up the calibration process. Should a technician try to calibrate this equipment by hand, it can often take 3 days and could produce inconsistent data findings. With automated test sequences in place, calibrations can take as little as three hours, reducing cost, turnaround time, and customer downtime. Accredited, automated calibration labs like Tektronix develop, maintain, and offer these automated test sets as standard practice.
Additionally, for high end T&M equipment, select a lab where experts can design new sequences when necessary. Small third-party calibration providers and in-house labs may not have this level of automation expertise and/or may not have equipment required to automate calibrations.
Multi-Site Consistency
Sensitive high-end electronic test and measurement equipment requires calibration to global standards like ISO 9001, z540.1, and ISO/IEC 17025. Your vendor should have documented test procedures for each standard and should be able to provide consistent calibrations across all their labs. Developing and automating test procedures allows for consistent, accurate results across sites. As an example of dedication to multi-site consistency and to prove compliance to international standards, Tektronix sends its equipment around the world to complete sample calibrations at each of its sites.
Selecting a Calibration Service Provider for High-End Equipment Calibration
In summary, if you are looking for a reliable calibration service provider that is qualified to calibrate high-end electronic test and measurement equipment, ensure your provider offers the right equipment, certified technicians, and procedures in place across all its facilities.
In addition, make sure you check the provider’s scope of accreditation to make sure the provider is accredited to perform the type of calibration you are looking for, and ask for a sample certificate with data to make sure the provider is checking all the test points recommended by the OEM.
Lastly, if you have a lot of equipment to calibrate, it’s okay to ask for a “try before you buy” option. Before you sign a contract with a calibration provider, make sure they can provide a high level of service by sending a small sample of equipment types in for service. Recently, a large telecom provider was searching for calibration services for hundreds of electronic test instruments as well as less sophisticated instruments like torque wrenches and pressure gauges. They were skeptical to use a multi-brand vendor like Tektronix because their internal engineers had assured the metrology department that the only way to receive a quality, accurate calibration was through the OEM for each piece of equipment.
To test the quality of calibration services from Tektronix, they sent 20 pieces of equipment to calibrate from multiple manufacturers including Rohde and Schwartz and Agilent. Unknown to Tektronix, many of those pieces were already known to be out of tolerance and need adjustments.
Tektronix performed ISO/IEC 17025 accredited calibrations on all the equipment provided, and successfully detected and documented 100% of the items that required adjustments. The customer was both surprised and satisfied with the accuracy and speed of the initial batch of calibrations and decided to make Tektronix its calibration partner.