How to Test EV Batteries with Accuracy, Precision and Speed
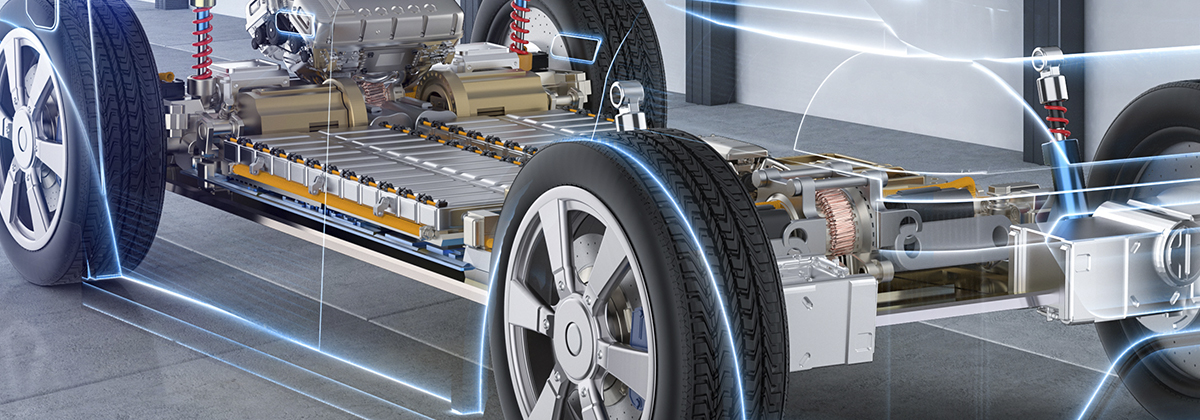
Batteries are evolving as quickly as technology is evolving. From mobile devices like smartphones and laptops to electric vehicles (EVs) and e-scooters, batteries must meet the ever-growing challenges – more storage and longer-lasting. However, no one chemistry or size fits all applications.
In fact, the world of batteries is complex, as myriad chemistries have advanced during the past few years, enabling manufacturers to narrow down their choice of chemistries.
While Lead-Acid batteries are standard with traditional automobiles using internal combustion engines (ICE) powered by conventional gasoline or diesel fuel, the popular chemistry for EV batteries today is Lithium-ion (Li-ion) for several reasons:
- High energy and power density
- Ability to extract energy quickly for vehicle acceleration
- Ability to charge the battery quickly
- Long cycle life, with fast charge and discharge characteristics
- EV range
Although Li-ion has several benefits as an EV battery, there is also a safety concern. Li-ion batteries can be a hazard if not properly engineered and manufactured because they have flammable electrolytes that can lead to explosions and fires if damaged or incorrectly charged. The good news is that much progress has been made recently in developing and manufacturing safe Li-ion batteries.
EV Battery testing challenges
To ensure reliable performance, EV batteries must be well-tested during development and production to ensure they will meet real-world demands. As a result, the EV battery testing equipment used for testing battery cells, modules and packs must be accurate, precise and reliable, with the ability to measure various performance characteristics using a single test instrument or system. Plus, any test protocols must be done with speed and agility, especially on the production floor, where any delays can add to the cost of production.
As EV growth accelerates, engineers must address new EV battery testing challenges, including higher voltage and power levels, increased energy density, space limitations, modular and scalable power, flexible configurations, wider operating envelopes and faster response times to emulate real-world conditions.
However, testing EV batteries with accuracy, reliability and safety is not trivial. Test engineers will confront numerous challenges. For example, it’s difficult to accurately measure high voltage, current and power capacity of battery cells, modules or battery packs and demonstrate the ability to reproduce data with high speed, precision and reliability. Additionally, the EV battery testing equipment must be capable of handling modular and scalable power with flexibility and faster time to market. The EV battery tester must deliver all these performances from a single integrated test piece.
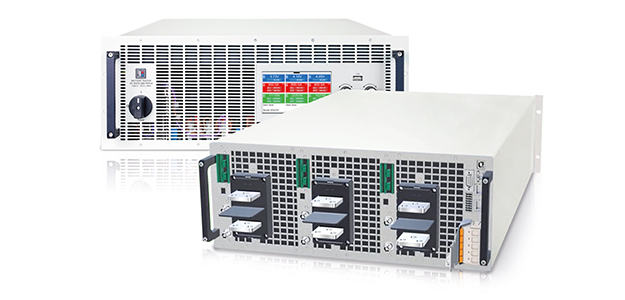
Figure 1. EA’s all-in-one test system EA-BT-20000 Triple Battery Tester.
To address these challenges, rely on the all-in-one EA-BT 20000 Triple Battery Tester (Figure 1). It is designed to simplify the engineer’s task of EV battery testing.
Building the EV battery testing infrastructure
Multiple EA-BT 20000 units can be combined into racks for measuring large-scale battery systems, generating up to 240 kW of testing capacity. These racks can be paralleled for increased load sharing and safety, with up to eight fully loaded test racks providing an impressive 1.92 MW of testing power.
In essence, EA’s integrated tester enables building a battery test infrastructure with safety and automation for testing cells, modules or battery packs.
Testing cells
For high-performance battery cell testing, rapid response time is crucial when testing individual cells. Also, Li-ion batteries are known for handling near-instantaneous load changes, making them suitable for quick power delivery applications. As a result, the EA-BT 20000 triple battery tester is unique as it can handle 1 ms changes in the load current draw. This feature accurately measures a cell’s dynamic response to fast load changes, often essential in real-world applications. Moreover, the EA-BT 20000 provides control of full current, even at low voltages. It can handle voltages as low as 2 V at full power, as you can still test at less than full power under 2V, ensuring that individual cells are tested accurately with speed and precision, even in high-power battery packs.
Testing modules
To ensure safe module testing, the EA-BT 20000 incorporates a pre-charge function. This feature safeguards both the DC programmable power supply and the battery being tested. Connecting a battery to the tester without pre-charging could result in power discharge, potentially damaging capacitors and causing sparks. The EA-BT 20000 mitigates these risks by pre-charging capacitors to match the battery’s voltage, ensuring safe and controlled testing conditions.
Additionally, the battery testing instrument features internal polarity detection, preventing incorrect connections to the battery. This added layer of protection safeguards against reversed polarity, which can have catastrophic consequences in a testing environment.
- Testing battery packs
The rise of EVs has led to the development of high-voltage battery packs. While most EV batteries operate from 350 V to 450 V, some high-performance models utilize 800 V or higher voltages. These higher voltage batteries enable faster charging, reduce cable weight and cut cable costs. The EA-BT 20000 is equipped to test high voltages effectively. Not only can it output high voltage (the Triple BT20000 the single channel can do up to 2000V), but it can also compensate for voltage drops in long cable runs (with remove voltage sense connected), ensuring accurate testing even in complex electric power delivery systems.
- Increased throughput
One of the most impressive aspects of the EA-BT 20000 is its ability to triple test throughput. Unlike traditional EV battery testing equipment that can only handle one device at a time, the EA-BT 20000 Triple 4U can simultaneously test three devices. This increased throughput reduces production costs and enhances testing capacity, a significant advantage in high-demand production environments such as rising EV battery testing.
- Cutting costs, saving energy
Cost efficiency is a crucial consideration in any testing environment. The EA-BT 20000 boasts an impressive energy-saving feature by returning up to 96% of absorbed energy to the grid during battery discharging. This energy recycling can lead to substantial utility cost savings, particularly when testing kW-capacity battery packs during extended production runs or when recycling.
Furthermore, the EA-BT 20000 is designed with high-power density, allowing it to deliver up to 30 kW of power per device. This space-saving design is a boon for test labs and production facilities where every inch of space is valuable.
To meet the needs of large-scale energy storage battery systems, multiple EA-BT 20000 units can be combined into racks, generating up to 240 kW of testing capacity. These racks can be paralleled for increased load sharing and safety, with up to eight fully loaded test racks providing an impressive 1.92 MW of testing power.
Protecting EV batteries
Because safety is critical in EV battery testing, EA-BT 20000 offers multiple layers of protection. During EV battery testing, polarity detection, overvoltage protection, overcurrent protection, overpower protection and overtemperature protection all work together to prevent damage to both the battery and the instrument. Each channel has a single wire K type thermocouple connection and warnings and alarms are generated if any parameter exceeds safe limits.

Benefits of multichannel tester
Capable of testing up to three battery cells, modules, or packs with an output of 4 kW/channel, 6 kW/channel or 10 kW/channel simultaneously (Figure 2), the EA-BT 20000 can test battery packs with 12 kW, 18 kW and 30 kW power capacity when connected in parallel. Plus, it is highly efficient, reducing test and investment costs and maximizing throughput.
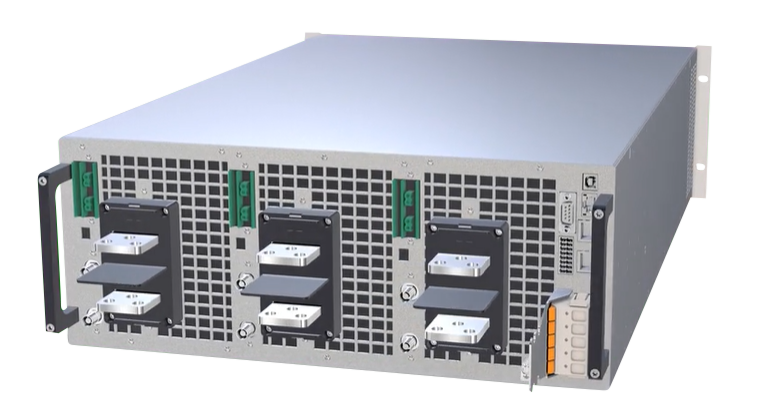
Figure 2. The power of three – EA-BT-20000 rear panel with three bus bar output channels for simultaneous testing of three batteries.
While designed for testing the electrical characteristics of a battery, the new tester EA-BT 20000 also lends itself to testing battery State-of-health (SOH) for second-life-classification and end-of-life (EOL) testing. It can be configured as an automated test system or an integrated battery tester.
While designed for testing the electrical characteristics of a battery, the new tester EA-BT 20000 also lends itself to testing battery State-of-health (SOH) for second-life-classification and end-of-life (EOL) testing. It can be configured as an automated test system or an integrated battery tester. Also, it can emulate battery resistance as single cells, modules, or packs.
- Reproducible data: The BT 20000 series is designed to provide reproducible data, which is essential for battery simulation. This ensures that the battery behavior is consistent and reliable.
- Protection for connected components: When used as a simulator, the BT 20000 series provides protection for the connected consuming component. This is similar to how a safety fuse operates.
- Overcurrent protection (OCP): The device features overcurrent protection that can switch off the output and generate an alarm, acting as a safeguard against excessive current that could damage the system.
- Voltage monitoring: The voltage can be monitored by the BT 20000 series, and if it goes over or under predefined limits, it can trigger various functions, as well as generate warnings and alarms.
- Flexible usability: The BT 20000 series is designed for flexible usability, which means it can be integrated into automated test systems or used in standalone battery tests, adapting to various simulation scenarios.
- Economical efficiency: The devices boast high efficiencies of up to over 96%, which makes them economical for long-term use in battery simulation applications.
These features collectively enable the BT 20000 series to effectively emulate batteries for the optimal configuration of energy storage systems and the components supplied under test. Further, it can be used for the optimal design of the energy storage system and the components to be tested. Finally, in the battery recycling phase, the tester can measure the complete discharge of the battery before final recycling.
Further, it can be used for the optimal design of the energy storage system and the components to be tested. Finally, in the battery recycling phase, the tester can measure the complete discharge of the battery before final recycling.
EV battery testing equipment for growing technology
Unlike conventional battery testers with single channel-single output, the new EA tester is unique with triple output and three-channel capability. Designed for a broader field of operation, the EA-BT 20000 tester features wide range input, 208 V – 480 V, +10%, three-phase ac, active power factor correction (typical 0.99), two-quadrant for charging and discharging, very high efficiency of up to more than 96% for energy recovery and saving, galvanically isolated share bus for parallel operation, master-auxiliary bus for parallel operation.
The EA-BT 20000 battery tester is the perfect EV battery testing equipment for modern EV batteries. Learn more here and contact us.