联系我们
与泰克代表实时聊天。 工作时间:上午 9:00 - 下午 5:00(太平洋标准时间)。
致电我们
工作时间:上午9:00-下午5:00(太平洋标准时间)
下载
下载手册、产品技术资料、软件等:
反馈
电动汽车电池测试——充满挑战的新世界
电动汽车电芯、电池模组和电池包生产系统依靠精密的电气仪器来可靠地识别变化。制造商依靠价格合理的测试设备:
- 持续检测微小的电气异常
- 集成到复杂多样的自动化系统中
- 随着测试要求的变化而调整
- 实现零停机
测试工程师正在与研发工程师密切合作,以实现新的电池技术。工程师们相信吉时利电动汽车测试设备可以帮助他们突破边界。
电动汽车电池技术和关键生产测试
用开路电压测试(OCV)对电池进行分级
只要看重电池性能的生产环境,电池分级都是其中的关键步骤。开路电压(OCV)的测量被用来将电池分为以下几个等级。
- A 级 电池的寿命最长,内部阻抗较低,整体性能更好。用于高功率应用,如电动汽车。
- B级 电池的性能较差,寿命较短。用于储能应用。
- C级 电池是性能最低的。用于单电池便携式应用。
制造商需要将最高质量的电池与可能存在内部缺陷(例如短路或污染物)的电池分开。可以监测电池OCV随时间的变化,来观察放电趋势并表征电池性能。可能需要数周时间才观察到OCV数十至数百微伏的变化。
吉时利的DMM7510是生产环境中OCV测试的完美解决方案。其7.5位的测量分辨率和超高精度意味着它可以测量更小的电压变化并更快得到结果。对于体量更大的应用,吉时利3706A系统开关和万用表允许在一个主机上有多达576个两线通道,在不挤占测试机架或工作台空间的情况下增强测试能力。
用电阻测量检查电池片和母线焊缝
焊接是自动化生产系统中的常见做法,用于将电池极耳连接到电极,以及将完整的电池连接在一起以形成电池包。大型电池包可以有数十到数百个焊缝或接头,将电池连接到母线。
质量好的焊点对电路的阻力很小,通常只有微欧姆。坏的焊缝或接头的测量值在毫欧范围内,这导致了性能问题和过多的热量产生,从而可能引发严重的热失控事件。几乎不可能肉眼识别出不良的焊缝。
然而,在生产环境中,通过使用精密数字万用表(如吉时利3706A系统开关和万用表)和电流源(如吉时利2460 SMU)进行电阻测量,可以快速识别焊接缺陷。源表可以提供高达7A的精确电流,而数字万用表可测量可低至微欧姆的接头电阻。3706A中内置的高密度开关可实现更多焊接检查,同时减少重新布线。
使用温度数据采集的环境和安全测试
环境测试是极其重要的,以确保电池在极端环境条件下的承受力和性能。热测试也是安全资质的一个重要组成部分。尽管温度测试因测试顺序、电池类型和物理约束条件而异,但电池的常见温度测量包括:
- 使用嵌入式传感器测量电池或模块的内部温度
- 电池或模块的外部温度
- 监测电池组周围的环境温度以了解散热情况或验证环境条件。
因为电池的性能取决于温度,在将电池安装进电动汽车时,工程师需要测量、记录电池的温度,在某些情况下还需要对电池的温度进行特性分析和编程。温度也是电池故障和热失控的指标。
吉时利3706A系统开关和万用表是一个高密度的开关系统,每个主机有多达576个2线通道。可自定义开关:将它配置为密度模式,添加更多监测点;或者配置为速度模式,进行快速温度检测。
用开路电压测试量化电池自放电情况
电池在没有连接的情况下,往往会随着时间的推移而放电,因为化学反应在内部慢慢逆转。理想情况下,这种内部自放电电流是非常小的,所以电池可以保持更长的续航时间。有内部缺陷的电池,如微短路、隔膜上的针孔和污染物,随着时间的推移会比高质量的电池放电更快。
这可能导致电池组的性能不佳和平衡问题,或导致电池受压。开路电压表 (OCV) 可用于监测自放电行为,因为电池放电时开路电压会降低。在装入电池组之前,要将完好的电池与有缺陷的电池分开。可能需要数周才能完成这项操作,因为需要这么久才观察到OCV数十到数百微伏的变化。
Keithley的DMM7510是利用OCV监测测量自放电的完美解决方案。7.5位数的分辨率和超高精度意味着它可以测量更小的电压变化并更快查看趋势。对于体量更大的应用,吉时利3706A系统开关和万用表允许在一个主机上有多达576个两线通道,在不挤占测试机架或工作台空间的情况下增强测试能力。
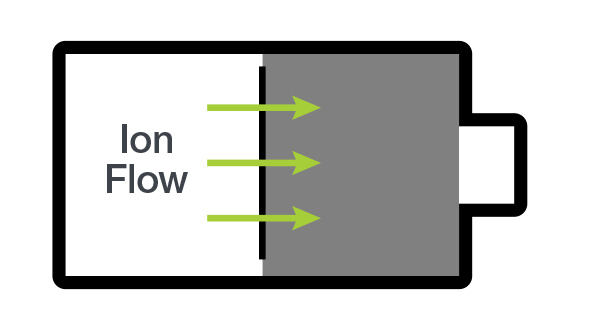
自放电是指即使在电池断开的情况下,离子仍在内部流动。
形成、老化和电池循环
电池制造过程中最重要的部分是化成和老化阶段,在此阶段电池中建立了关键的化学机制。这一过程的结果直接影响到电池以后的性能。化成后要测试哪些电池化成失败。老化后可进行EOL测试(寿命终止测试),以评估电池寿命并进行质量控制。
化成和老化要求电池以不同的速度反复充电和放电。电池循环充放电亦是许多其他测试中的一个重要组成部分,包括建模和热特性分析。
测试流程差别很大,取决于电池的化学成分、结构和测试概况。而且许多其他测试需要对电池循环充放电,所以测试方案必须灵活。
吉时利源表提供 了方便的一体化充放电解决方案。2400系列图形触摸屏源表提供高达7A的精确直流电源。这些源表搭载 TSP® 脚本技术 ,使生产自动化变得简单而高效。
用直流内阻确保电池质量
高内阻的电池性能较低,发生热失控等故障的风险较高。内阻是固态电解质膜(SEI)形成不正确的指标,也可以作为电池质量的衡量标准。
吉时利源表为直流内阻测试提供了一体化解决方案。2400系列图形触摸屏SMU可以产生精确的低电流,并测量相应的电压以计算内阻。
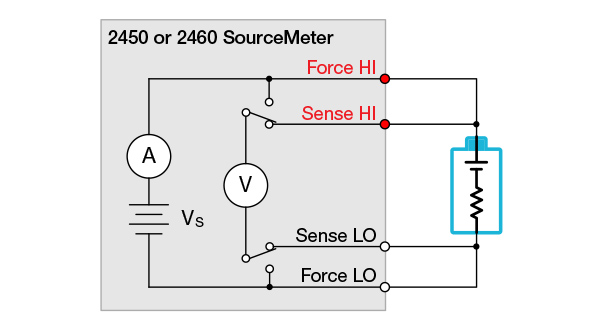
使用源表测量电池的直流内阻。
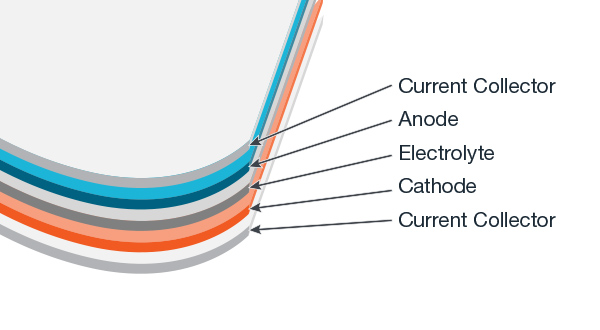
电池中的层结构。测量电极材料和集电体之间的接触电阻。
通过低电阻测量检查电极接触质量
集电器和卷到集电器上的电极材料之间的连接不良会增加电池的内阻。尽早识别不良电极可在生产过程中节省时间和资源。
吉时利 6200 系列敏感电流源 与 2182A纳伏表 搭配,是对电极进行灵敏低电阻测量的完美组合。这种组合可以测量低至几十纳欧的电阻,从而在最大程度上确保电极的质量。
通过测量绝缘电阻保持电池绝缘
电池短路意味着危险故障的风险短路可能发生在内部,但当绝缘失效或电池组连接不正确时,也有外部短路的风险。验证电池电极与地面的隔离以及暴露在电流中的任何材料的绝缘质量可以防止以后出现严重的故障。
吉时利2470高压源表为测量材料的电阻提供了简单的一体化解决方案。SMU可以提供高达1kV的电压源并计算出材料的相应电阻。
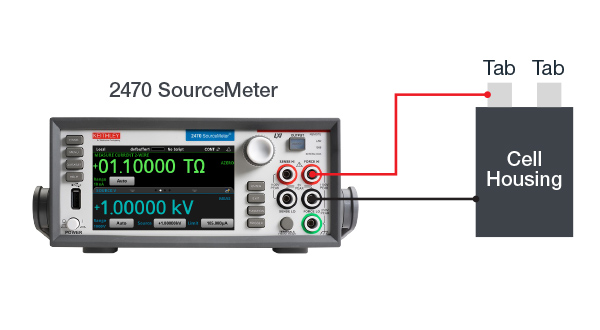
测量绝缘电阻。电池极耳应与外壳电气隔离。
电动汽车电池测试常见问题
什么是电动汽车电池测试?
电动汽车电池测试采用多种方法验证电池的性能和安全性。测试贯穿于电池生命周期的各个阶段,从设计实验室到生产车间,再到最终用户。
如何对电动汽车电池进行测试?
电动汽车电池要经过各种测试,包括化学、机械、热和电气测试。电气测试包括测量电池电压、内部阻抗、元件电阻和充放电曲线。电气测试设备可以是 仅用于测量的 DMM,也可以是能够进行精确供电和测量的 电源和源测量单元 (SMU)。
电动汽车电池测试的标准是什么?
电动汽车电池测试有许多标准,涉及从电芯到电池包的安全和性能。标准还取决于最终用途。例如,民用电动汽车的标准可能与工业电动汽车或电动自行车和电动摩托车等小型交通工具的标准不同。
电动汽车电池测试为何重要?
全面的测试可确保电池不仅安全,而且符合制造商设定的性能规格。低质量电池会对整个电池包产生连带影响,因此一定要在最终用户使用电池之前识别出它们。研发阶段的测试也对验证新设计和改进设计至关重要。
电动汽车电池应满足哪些要求?
电池涉及复杂的指标,包括电压、电流、阻抗、容量和寿命。额定值取决于电池的化学成分和结构。通过电气测试验证此类额定值,对于最终用户非常重要。