Electromagnetic compatibility (EMC) and the related electromagnetic interference (EMI) seems to be one of those necessary evils that must be overcome prior to marketing commercial or consumer electronic products, as well as military and aerospace equipment. Unfortunately, few universities and colleges teach this important information, with the result that products are rarely designed to meet EMC/ EMI requirements. EMC or EMI compliance is often left to the end of a project with all the associated schedule delays and unplanned cost.
The purpose of this application note is to help product designers or EMC engineers learn enough basics of EMC and EMI so that the usual design failures are addressed early when costs and design is minimized. Achieving EMC/EMI is easy once these basics are understood. This application note will also focus on measuring and mitigating radiated and conducted emissions using Tektronix EMCVu EMI software.
Briefly, radiated emissions is a measure of the radiated E-fields, while conducted emissions is a measure of the conducted EMI currents emanating from the product, equipment, or system under test. There are worldwide limits on how high these emissions can be, depending on the environment in which the equipment is designed to work.
Today, with all the myriad electronic products, including wireless and mobile devices, compatibility between devices is becoming even more important. Products must not interfere with one another (radiated or conducted emissions) and they must be designed to be immune to external energy sources. Most countries now impose some sort of EMC standards to which products must be tested.
Basic Definitions
Let's start with some basic definitions, and there's a subtle difference. EMC implies that the equipment being developed is compatible within the expected operating environment. For example, a ruggedized satellite communications system when mounted in a military vehicle must work as expected, even in the vicinity of other high-powered transmitters or radars. This implies both emissions and immunity in close environments. This usually applies to military and aerospace products and systems, as well as automotive environments.
EMI (also sometimes referred to as radio frequency interference, or RFI) is more concerned with a product interfering with existing radio, television, or other communications systems, such as mobile telephone. It also includes immunity to external energy sources, such as electrostatic discharge and power line transients. This usually applies to commercial, consumer, industrial, medical, and scientific products.
Why Do Products Radiate?
So, why do electronic products radiate? It's all about controlling the energy from internal sources from coupling to system cables (I/O or power) or slots/seams if using shielded enclosures.
For example, the most common issue for most products is radiated emissions. We generally have several energy sources on our PC boards, and somehow, these energy sources couple harmonic currents to an "antenna-like structure", such as an I/O cable. See Figure 1.
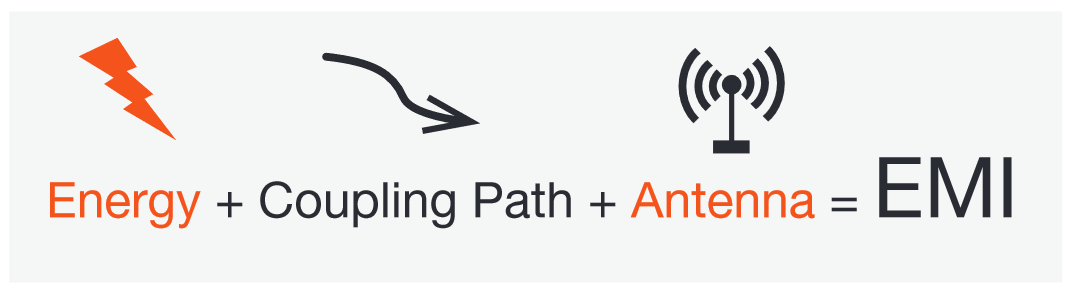
Internal energy sources might include high frequency clocks or any high speed, fast-edged digital signal. These may be transferred via conduction, radiation, inductive, or capacitive coupling mechanisms. For example, a common situation is harmonics of a fast-edged clock (say an Ethernet clock) coupling to an I/O cable, which acts as an antenna and radiates. If these harmonic emissions exceed certain compliance test limits, the product fails and must be redesigned to reduce or eliminate the emission. In a like manner, energy sources may couple to power cables and create conducted emissions into the AC (or DC) power line.
Common Product Design Issues
We'll start by describing some common product design issues to be aware of during product development. If these design areas are addressed well in advance during the product development cycle, costs and related EMC troubleshooting and compliance testing will be minimized.
Cable shield termination – By far the most common issue causing radiated emissions is I/O or power cables merely penetrating through shielded enclosures. This occurs when cable connectors are soldered to PC boards and the board mounted inside the enclosure. Once a cable is plugged in to the connector, it effectively penetrates the shield allowing EMI noise currents to flow out along the outside of the shield and then radiate like an antenna. To mitigate this, the cable shield needs to be bonded (ideally a 360-degree connection) to the shielded enclosure. Bulkhead connectors will resolve this or some PC board mount connectors have built in EMI gaskets that press up to the inside of the enclosure.
Leaky shielded enclosure seams or apertures – The next most common issue is simply areas where enclosure seams are not well bonded or aperture areas in the sheet metal where keyboards or displays are mounted. Mitigating this usually requires a more robust mechanical design or the addition of EMI gasketing to bond seams or gaps.
Lack of filtering for I/O or power cables – Many commercial or consumer products can't justify shielded enclosures and so the first line of defense must include adequate differential mode and common mode filtering right at the I/O and power connectors of the PC board. High-speed clock signals or noisy internal cables must be routed well away from I/O and power connectors.
Poor PC board design – Many emissions problems can be mitigated by proper PC board design. Common design issues include:
- Poor layer stack-up – All layers with high-speed signals or clocks are transmission lines must have an adjacent ground return plane. In addition, all power traces (or planes) must have an adjacent return plane, since the power distribution network (PDN) is considered a transmission line, as well.
- Gaps in ground return planes - All return planes must be solid, without large gaps or slots. When a high-speed signal or clock trace crosses a gap in the return plane, it creates large amounts of common mode currents, which can propagate throughout your PC board and internal cables. If the I/O or power cables are not properly filtered or if the I/O or power cable shields are not properly terminated to a shielded enclosure, then these cables tend to radiate and may cause emissions failures.
- Poor layout of circuit functions – Digital, analog, motor control, and wireless circuitry should be well isolated from each other within the PC board real estate. For example, you wouldn't want return currents from the motor control circuitry passing through sensitive analog circuit returns. Likewise, on-board DC-DC converter currents should be restricted to just a small area and away from other circuitry.
Pre-Compliance versus Compliance Testing
While investing in your own full in-house compliance EMC test laboratory may seem difficult to justify, most companies should be able to implement an affordable pre-compliance testing capability. Outside compliance test labs can cost upwards of $2,000 per day. The advantage of being able to perform some of the key tests in-house is that you can quickly determine whether your product is close to passing.
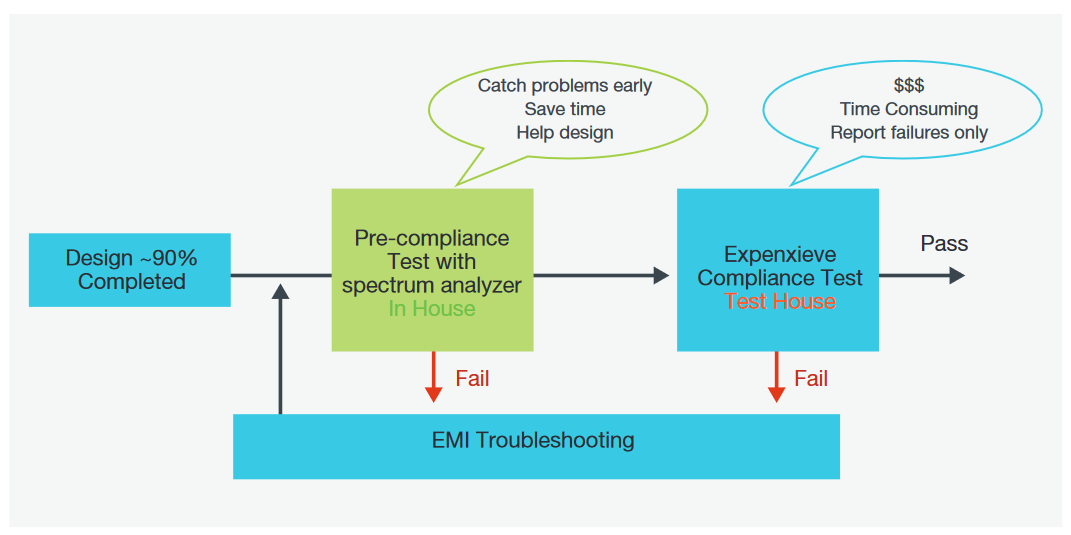
A suggested product design workflow is pictured in Figure 2. Once the product emissions are characterized and mitigated, then it's off the third-party test house for compliance testing.
Many companies work for weeks or months to beat down a radiated emissions problem by repeatedly cycling between their R&D lab and third-party compliance test lab. This is very frustrating for both the designers and their management. By performing some very quick and simple tests, you can identify failures, narrow down the root cause, and try various fixes well before taking the product in for full compliance testing. Tektronix offers some affordable spectrum analyzers and software, such as EMCVu, to make this job fast and easy.
EMI Troubleshooting versus Pre-Compliance Testing
There's a difference between general troubleshooting or debugging EMI issues and pre-compliance testing. General troubleshooting is usually performed with a set of specialized probes and a spectrum analyzer. The goal is to identify sources of harmonic energy and determine fixes that reduce the harmonic amplitudes. Here, we're mainly looking for relative changes.
Pre-compliance testing, on the other hand, attempts to duplicate the way the compliance tests are run to the best ability possible and to compare with actual test limits. This requires a calibrated EMI antenna and knowledge of the gains or losses in the measurement system.
For best results, the radiated emissions test is usually performed inside a semi-anechoic chamber in order to eliminate outside received signals (ambients), such as broadcast radio, television, two-way radio, or cellular telephone. However, this can be relatively expensive, so most in-house pre-compliance tests are normally set up outside a shielded chamber and special techniques are used to separate ambient signals from those emanating from the product under test.
Real-Time Spectrum Analysis
The latest tool for serious EMI troubleshooting or debugging has become the real-time (RT) spectrum analyzer. Because manufacturing costs have been decreasing, some RT analyzers are becoming more affordable than ever. In this section, we'll show you the advantages in using RT analysis for observing and troubleshooting unusual EMI.
First, let's review the differences between the conventional swept and real-time spectrum analyzers. You might also refer to the system block diagrams in Figure 3. We'll also briefly mention EMI receivers.
Swept-tuned analyzer – The swept analyzer uses a tunable local oscillator (LO) in a standard superhetrodyne circuit. It can sweep over a specified frequency range using a userselected resolution (or "receiver") bandwidth. RF signals introduced to the input port are mixed with the local oscillator and the specified frequency span (stop frequency minus start frequency) is displayed as RF power or voltage versus frequency. The only time data is captured is during the sweep time. After the frequency sweep, the captured data is processed and displayed. There is usually significant delay (or "dead" time) between sweeps, so it's quite possible for the analyzer to miss capturing intermittent or fast-moving signals. Also, most digitally-tuned swept analyzers can only display a fixed number of tuning steps. For example, for the typical radiated emissions test, the resolution bandwidth is set to 120 kHz. If the display uses 1000 display points and you set the span from 30 to 1000 MHz (970 MHz span), the step size will be about 1 MHz apart, with a chance of missing signals in between.
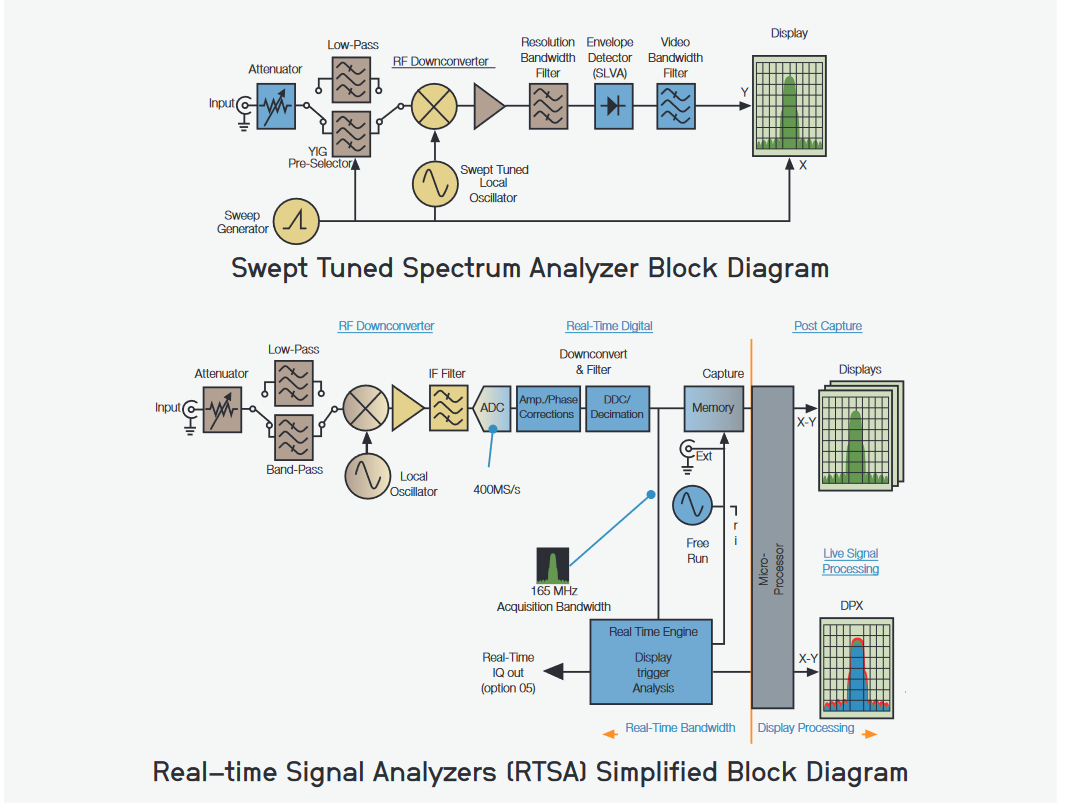
EMI receiver – An EMI receiver uses a tuned local oscillator front end with tracking pre-selection filters, similar to an AM/ FM broadcast radio. There are many advantages, but the primary ones include a continuously-tuned receiver, so the chances of missing signals due to stepped-tuning across a frequency span is eliminated. Also, the preselection filters reduce the chance of strong signals outside the frequency span from interfering with an accurate amplitude measurement, something you need to be aware of with swept-tuned and realtime analyzers with "wide open" RF inputs.
Real-time analyzer – A real-time (RT) analyzer uses a stationary LO, looks at narrow windows of bandwidth (realtime bandwidth), and digitizes the incoming spectrum. This digitized spectrum is stored in a time record buffer and held for processing by the FFT algorithm. Ideally, once digitized, FPGAs process FFTs at a rate equal, or faster, then the collection rate. However, this collection rate depends on the span and resolution bandwidth. The major difference between the swept-tuned analyzer and real-time analyzer is the sheer number-crunching ability of the real-time calculation, as well as a fast graphics processor, which allows for a data-dense display of various frequency-versus-time presentations and digital demodulation.
One advantage of a RT analyzer is the ability to capture RF pulses as short as 20 us, digital modulations, and other pulsing or fast changing signals. In addition, they can capture and process data much faster than swept analyzers – there's no need to wait seconds or minutes to capture a spectrum in Max Hold mode. This allows very fast troubleshooting since you can see the result of fixes immediately. Finally, the RT analyzers have an addition feature called a spectrogram (or "waterfall") display, where signal amplitudes are shown versus time. This is a great feature allowing you to determine the timing of intermittent EMI. Tektronix RT-series analyzers also offer up to 8000 display points across a set span, so the chances of missing signals in between frequency steps is greatly reduced.
For the example shown, we'll be using the Tektronix RSA306B real-time USB-controlled spectrum analyzer (Reference 1) with Tekbox Digital Solutions near field probes (Reference 2).
Figure 4 shows a typical advantage of the RT display over that of the swept display. Here, we see some broadband motor noise completely masking several narrow band harmonics. The swept analyzer has trouble capturing the motor noise, but we can see occasional captures indicating there was "something" there. Switching to Max Hold mode and waiting a few minutes will help fill in the swept display, but then you'd miss seeing the narrow band emissions.
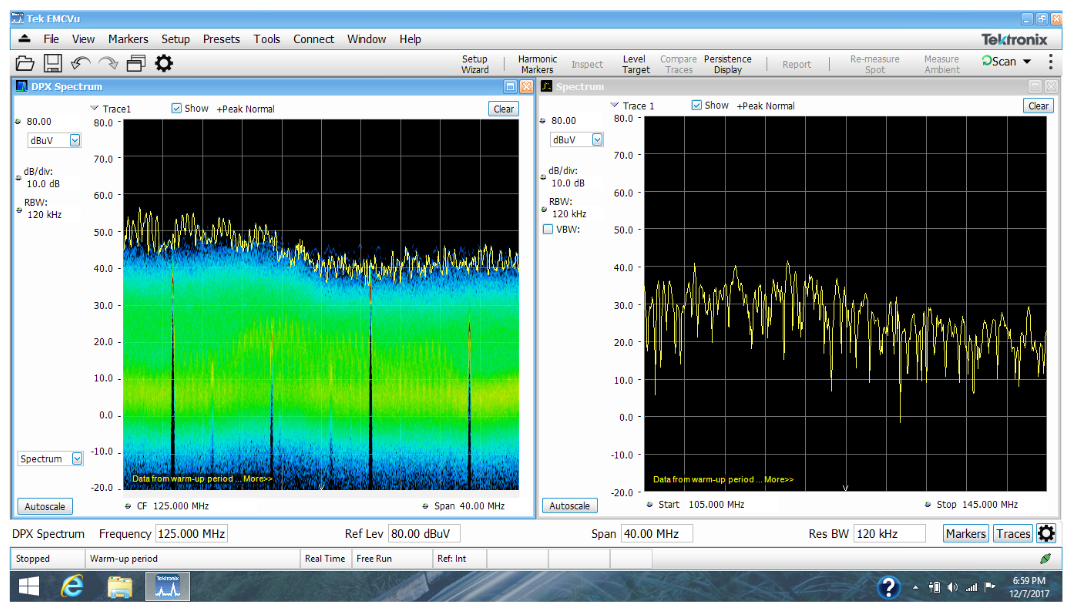
Most RT analyzers will also have optional EMI software that will help collect data or even perform pre-compliance testing for radiated and conducted emissions. For example, Tektronix offers their SignalVu-PC software with the RSA306B, but also recently announced their EMI troubleshooting and precompliance software for the RSA-series, called "EMCVu". EMCVu includes some impressive EMI troubleshooting and pre-compliance test features and can switch from one mode to the other quickly. It comes with pre-defined transducer factors (antenna and cable loss tables), CISPR and FCC limit lines, and easy report generation. In pre-compliance mode, it can scan the entire frequency range in a few seconds, numbering all the harmonics above the limit and within a certain margin to the limit. These captured harmonic signals can then be examined more closely and then switched over to troubleshooting mode to try various fixes. We'll be using EMCVu for basic troubleshooting or debugging emission issues for this application note.
How Can Real-Time Analyzers Help Troubleshoot EMI?
So, let's turn our attention back to probing the PC board and cables. How often have you probed, troubleshot, and fixed a product only to have it fail at the compliance test facility? Many of today's products, especially mobile products, include on board DC-DC converters that produce a very broadband EMI spectrum out past 1 GHz that can impact the operation of cellular or GPS wireless receivers. In addition, digital processors can change emission characteristics with time or operating mode. Add wireless features and you have a myriad of potential energy sources that can change emission characteristics with time.
We'll demonstrate an example where swept analyzers might very well miss a bursting increase in emissions or fail to capture broadband EMI that is greater in amplitude than the usual narrow band harmonics we're all used to.
EXAMPLE - PULSATING BROADBAND HARMONIC EMI
Most of the time, you'll find narrow band harmonics are relatively stable in amplitude. However, there are times when the amplitude can change, due to gated digital signals or different operating modes. If the harmonic peaks upward at the wrong time, it can lead to compliance failures.
Swept analyzers can easily miss these infrequent amplitude peaks. Placing the swept analyzer in "Max Hold" mode can help, but it could take several minutes to capture the peak of the emission. Even so, peaks can be missed, due to dead time in between scans.
RT analyzers, on the other hand are adept at capturing fast changing signals. Here's an example where we're measuring the narrow band low frequency emissions from an on-board DC-DC converter on a small mobile device (Figure 5).

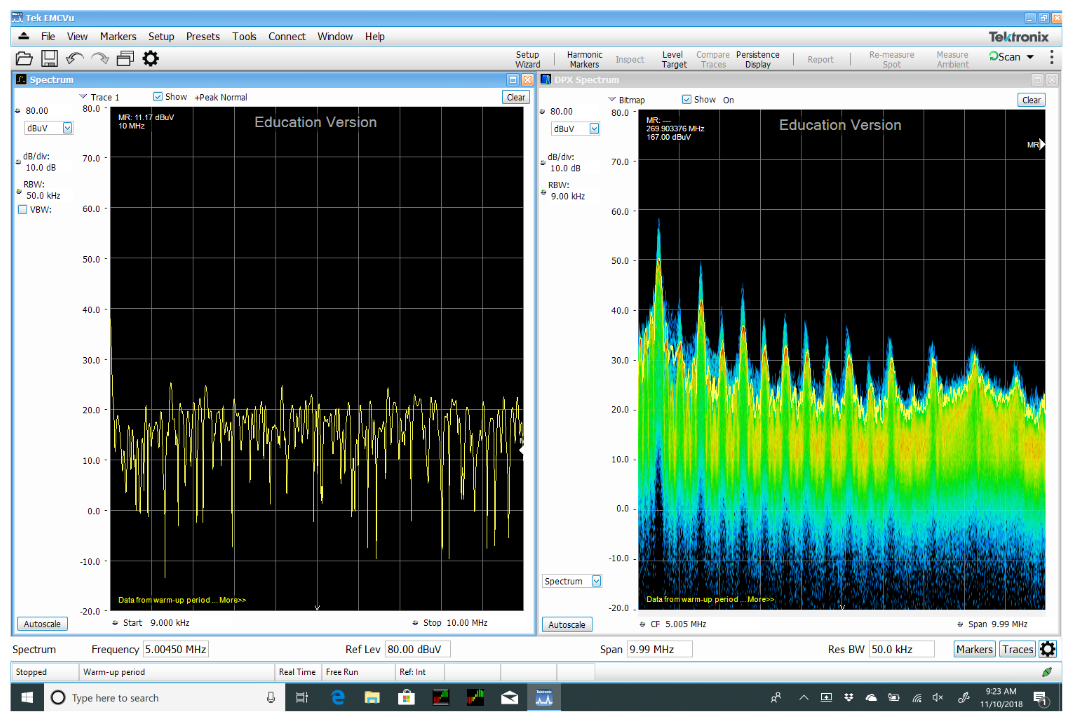
In Figure 6, we're looking from 9 kHz to 10 MHz and we see the swept measurement is even having a hard time capturing the regular peak emissions, while the RT measurement captures the peaks easily and even detects an occasional six dB pulsing increase in amplitude (as shown in the blue persistence display). That infrequent pulsing amplitude increase could easily cause a compliance failure should it couple out through conduction or radiation.
Developing Your Own EMI Troubleshooting and Pre-Compliance Test Lab
So, what's involved in developing a basic EMI troubleshooting and pre-compliance test lab? It's not nearly as expensive as you might think. See Figure 7 for examples.
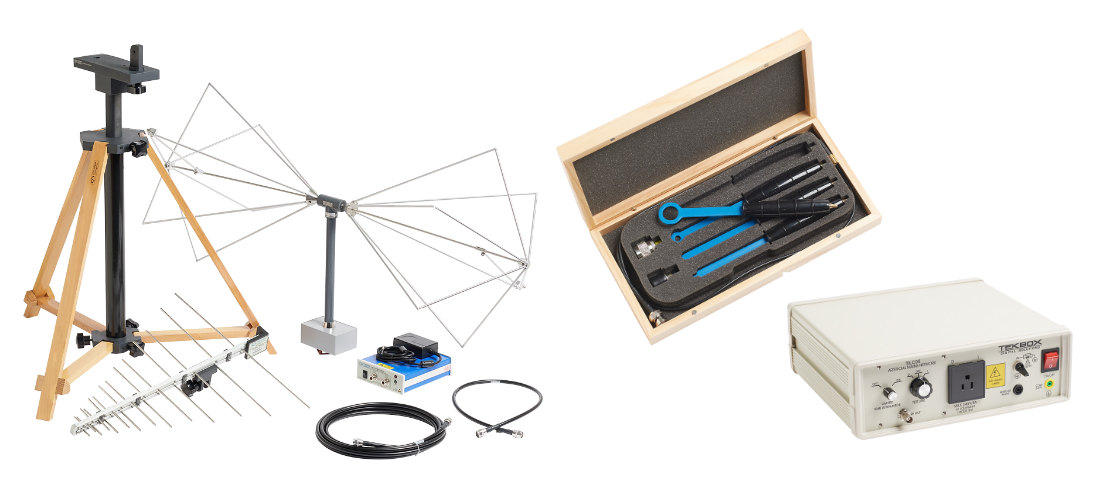
Here is a list of basic equipment required for these tests:
Radiated Emissions – While an oscilloscope is very useful for determining rise times and ringing, a spectrum analyzer is really the desired instrument for most EMI troubleshooting and measurement. In addition, you'll want a set of nearfield probes, a current probe, a calibrated (or uncalibrated – see below) EMI antenna, and possibly a 20 to 30 dB gain broadband preamplifier to boost the signal from the smaller probes or antenna.
Conducted Emissions – A spectrum analyzer and line impedance stabilization network (LISN) are generally all that's required. In some cases, a transient suppressor and/or 10 dB attenuator is used as additional protection for the analyzer (see sidebar warning near the end). The test is required to be performed above a large ground plane.
Generally, most pre-compliance testing does not require very expensive equipment, but you may wish to factor in some niceties, such as real-time spectrum analysis for signals that may only appear infrequently or signals, such as wireless communications, that may not display clearly on low-cost swept analyzers. For example, the Tektronix RSA-series spectrum analyzers all have real-time measurement features. In addition, there may be important reasons to stick with higherend lab-quality equipment with their higher measurement performance, such as the Tektronix RSA5000-series benchtop analyzer.
EMI Troubleshooting
THREE-STEP PROCESS FOR EMI TROUBLESHOOTING
Here's a simple three-step process for EMI troubleshooting, which we'll briefly explain below. We'll use Tektronix EMCVu as an example. You'll want to download the free "EMI Pre-Compliance Test Guide" for more details on this troubleshooting process (Reference 5).
Step 1 – Use near field probes (either H- or E-field) to identify energy sources and characteristic emission profiles on the PC board and internal cables. Energy sources generally include clock oscillators, processors, RAM, D/A or A/D converters, DC-DC converters, and other sources, which produce high frequency, fast-edged, digital signals. If the product includes a shielded enclosure, probe for leaky seams of other apertures. Record the emission profile of each energy sources.
Step 2 – Use a current probe to measure high frequency cable currents. Remember, cables are the most likely structure to radiate RF energy. Move the probe back and forth along the cable to maximize the highest currents. Record the emission profile of each cable.
Step 3 – Use a nearby antenna (typically, a 1m test distance) to determine which of the harmonic content actually radiates. Catalog these harmonics and compare to the internal and cable measurements. This will help you determine the most likely energy sources that are coupling to cables or seams and radiating. We'll go over this procedure in more detail later.
Radiated Emissions is normally the higighest risk test. Set up your spectrum analyzer as follows:
- Frequency 10 to 500 MHz
- Resolution bandwidth = 100 or 120 kHz
- Adjust the Reference Level so the highest harmonics are displayed and the vertical scale is reading in even 10 dB increments
- Use positive peak detection
Setting the vertical units from the default dBm to dBμV is preferable, so the displayed numbers are positive. This is also the same unit used in the test limits of the standards. Setting the horizontal scale from linear to log is helpful for visually interpreting spot (harmonic) frequencies.
You might start by performing an initial scan up to 500 MHz, because this is usually the worst-case band for digital harmonics. You'll want to also record the emissions at least up to 1 GHz (or higher) in order to characterize any other dominant emissions. Generally speaking, mitigating the lower frequency harmonics will also reduce the higher harmonics.
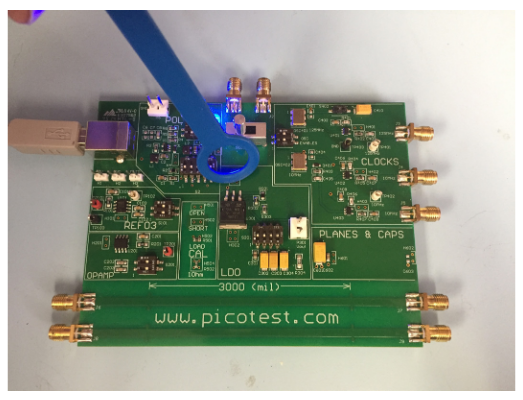
STEP 1 - Near Field Probing - Most near field probe kits come with both E-field and H-field probes. Deciding on H-field or E-field probes depends on whether you'll be probing currents – that is, high di/dt – (circuit traces, cables, etc.) or high voltages – that is, dV/dt – (switching power supplies, etc.) respectively. Most troubleshooting is done with H-field probes. The smaller diameter ones are higher resolution but may need preamplification to boost their signals. However, both H- and E-field probes are useful for locating leaky seams or gaps in shielded enclosures.
Start with the larger H-field probe (Figure 8) and sniff around the product enclosure, circuit board(s), and attached cables. The objective is to identify major noise sources and specific narrow band and broadband frequencies. Document the locations and dominant frequency characteristics observed. As you zero in on sources, you may wish to switch to smallerdiameter H-field probes, which will offer greater resolution (but less sensitivity).
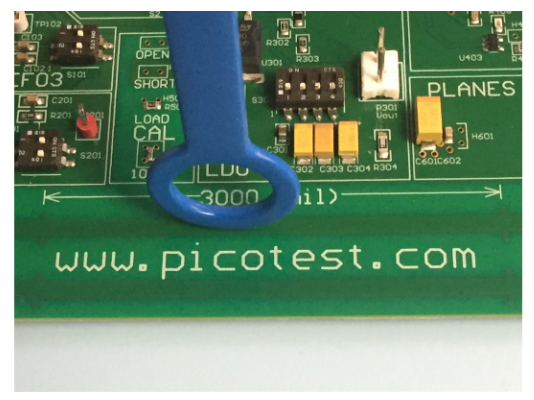
Also, note that H-field probes are most sensitive (will couple the most magnetic flux) when their plane is oriented in parallel with the trace or cable. It's also best to position the probe at 90 degrees to the plane of the PC board. See Figure 9.
Remember that not all sources of high frequency energy located on the board will actually radiate! Radiation requires some form of coupling to an "antenna-like" structure, such as an I/O cable, power cable, or seam in the shielded enclosure.
When applying potential fixes at the board level, be sure to tape down the near field probe to reduce the variation you'll experience in physical location of the probe tip. Remember, we're mainly interested in relative changes as we apply fixes.
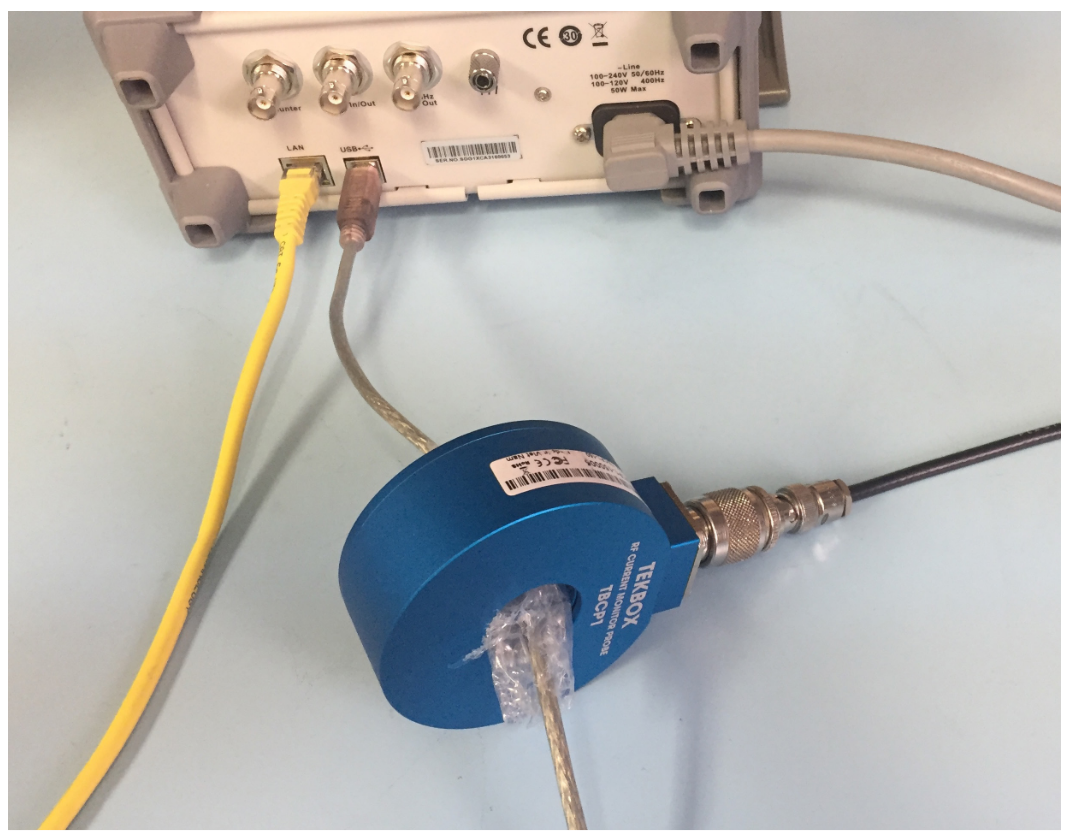
STEP 2 - Current Probe Measurements - Next, measure the attached common mode cable currents (including power cables) with a high frequency current probe, such as the Tekbox TBCP1-150, or equivalent (Figure 10). Document the locations of the top several harmonics and compare with the list determined by near field probing. These will be the most likely to actually radiate and cause test failures because they are flowing on antenna-like structures (cables). Use the manufacturer's supplied calibration chart of transfer impedance to calculate the actual current at a particular frequency. Adding a bit of "bubble wrap" around the cable being measured will help center it within the probe for best accuracy. Note that it only takes only 5 to 8 μA of high frequency current to fail the FCC or CISPR test limits. Using the manufacturer's supplied transfer impedance curve will help you calculate the current from the analyzer voltage.
It's a good idea to slide the current probe back and forth to maximize the harmonics. This is because some frequencies will resonate in different places, due to standing waves on the cable.
It's also possible to predict the radiated E-field (V/m) given the current flowing in a wire or cable, with the assumption the length is electrically short at the frequency of concern. This has been shown to be accurate for 1m long cables at up to 200 MHz. Refer to Reference 1, 2, or 5 for details.
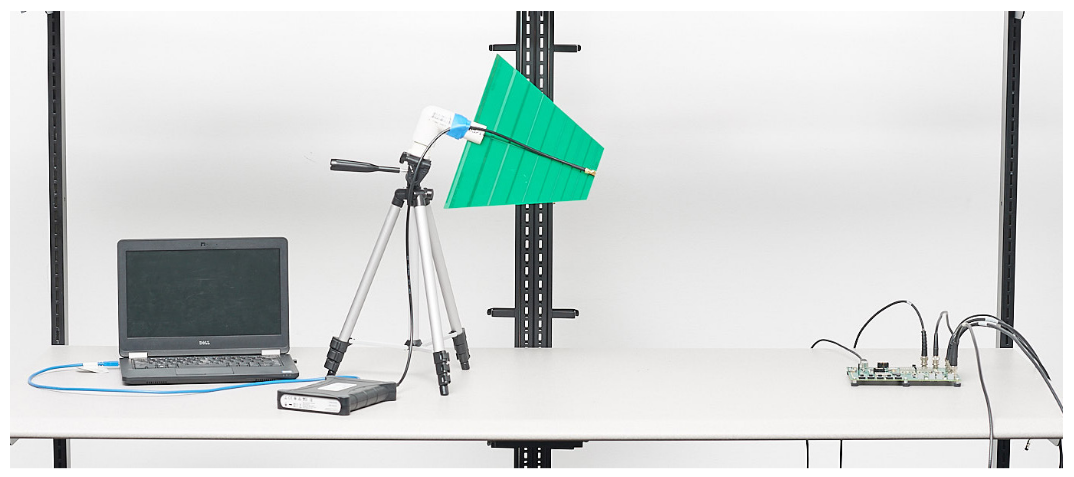
STEP 3 - Troubleshooting with a Close-Spaced Antenna - Once the product's harmonic profile is fully characterized, it's time to see which harmonics actually radiate. To do this, we can use an uncalibrated antenna connected to a benchtop spectrum analyzer spaced at least 1m away from the product or system under test to measure the actual emissions (Figure 11). Typically, it will be radiation from attached I/O or power cables, as well as leakage in seams or apertures of the shielded enclosure. Compare this data to that of the near field and current probes. Can you now determine the probable source(s) of the emissions noted?
Try to determine if cable radiation is the dominant issue by removing the cables one by one. You can also try installing a ferrite choke on one, or more, cables as a test. Use the near field probes to determine if leakage is also occurring from seams or openings in the shielded enclosure.
Once the emission sources are identified, you can use your knowledge of filtering, grounding, and shielding to mitigate the problem emissions. Try to determine the coupling path from inside the product to any outside cables. In some cases, the circuit board may need to be redesigned by optimizing the layer stack-up or by eliminating high speed traces crossing gaps in return planes, etc. By observing the results in real time with an antenna spaced some distance away, the mitigation phase should go quickly.
Analyze the Data
Remember that not all near field signals will couple to "antenna-like" structures and radiate. Use a harmonic analyzer tool in EMCVu to help identify harmonics belong to specific energy sources. Note that in many cases, two, or more, sources will generate the some (or all) the same harmonics. For example, a 25 MHz clock and 100 MHz clock can both produce harmonics of 100, 200, 300 MHz, etc. Oftentimes, you'll need to fix more than one source to eliminate a single harmonic. EMCVu includes some powerful data capture and documentation features that will help speed up the data collection process from steps 1 through 3.
After the harmonics are analyzed and you have identified the most likely sources, the next step is to determine the coupling path from source and out the product. Usually, it's the I/O or power cables that are the actual radiating structure. Sometimes, its leaky seams or apertures (display or keyboard, for example).
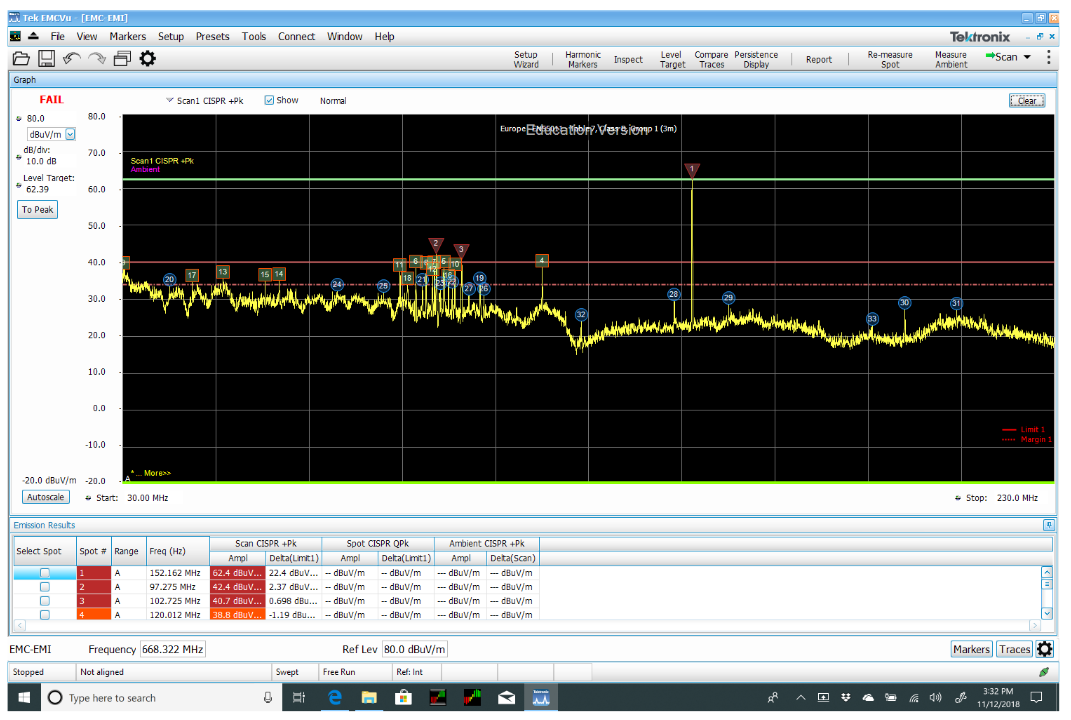
There are four possible coupling paths; conducted, radiated, capacitive, and inductive. The latter two (capacitive and inductive) are so-called; "near field" coupling and small changes in distance between source and victim should create large effects in radiated energy. For example, a ribbon cable routed too close to a power supply heat sink (capacitive coupling or dV/dt) and causing radiated emissions can be resolved merely by moving the ribbon able further away from the heat sink. The inductive coupling (di/dt) between a source and victim cable can also be reduced by rerouting. Both these internal coupling mechanisms (or similar PC board design issues) can lead to conducted (out power cables) or radiated (I/O or power cables acting as antennas or enclosure seams/ apertures) emissions.
In many cases, its simply poor cable shield bonding to shielded enclosures or lack of common-mode filtering at I/O or power ports that lead to radiated emissions.
One handy troubleshooting technique that can save time is the use of the Level Target line. To activate this, click on Level Target in the upper tabs. This is a user settable reference line that can be set to the peak of a spot frequency and during the troubleshooting process, you be able to see at a glance whether the resulting fix is helping or hurting. See Figure 12 for an example. Here's we've narrowed in on just the frequency band 30 to 230 MHz and have adjusted the Level Target to the highest spot frequency of 152.162 MHz. At this point try applying fixes to check the effect on the amplitude of this spot frequency
A Note on the Use of External Antennas
There are two distinct use models when using external EMI antennas:
- Relative troubleshooting, where you know areas of failing frequencies and need to reduce their amplitudes. A calibrated antenna is not required, as only relative changes are important. The important thing is that harmonic content from the EUT should be easily visible.
- Pre-compliance testing, where you wish to duplicate the test setup as used by the compliance test lab. That is, setting up a calibrated antenna 3m or 10m away from the product or system under test and determining in advance whether you're passing or failing.
Many times, when troubleshooting emissions, you may already have run a pre-compliance (or formal) test and know how far over limit the harmonics are. So, when troubleshooting, the important point is that the measurements are generally relative, rather than absolute. That is, if we know certain harmonics are 5 to 10 dB over the limit, the goal would be to reduce these by at least that, or more, for decent margin. Therefore, a calibrated antenna is not required, as only relative changes are important. The antenna also does not necessarily need to be tuned to the frequency of the harmonics. Almost any "hunk of metal" connected to the spectrum analyzer should work. The important thing is that harmonic content from the EUT should be easily visible.
Pre-Compliance Testing
We'll first describe how to perform the pre-compliance test for radiated emissions, as that is the most likely test failure for products. After that, testing for conducted emissions will be described with less detail, because the process is essentially the same. During setup, you'll select Conducted Emissions and choose the appropriate standards and limits.
PRE-COMPLIANCE TESTING FOR RADIATED EMISSIONS
The goal of pre-compliance testing is to duplicate the test setup as used by the compliance test lab. Pre-compliance testing for radiated emissions requires a calibrated EMI antenna positioned 3m or 10m away from the product under test. This way, you'll be able to compare the emissions with actual test limits according to the appropriate standards used. The test may be set up in any area large enough to avoid reflections and far away from other equipment that could interfere with the testing. Sometimes a parking lot is used. One example could be a large conference room (Figure 13).
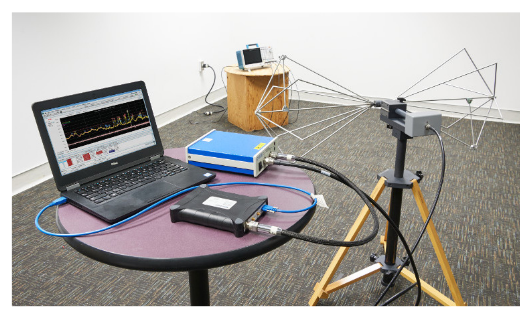
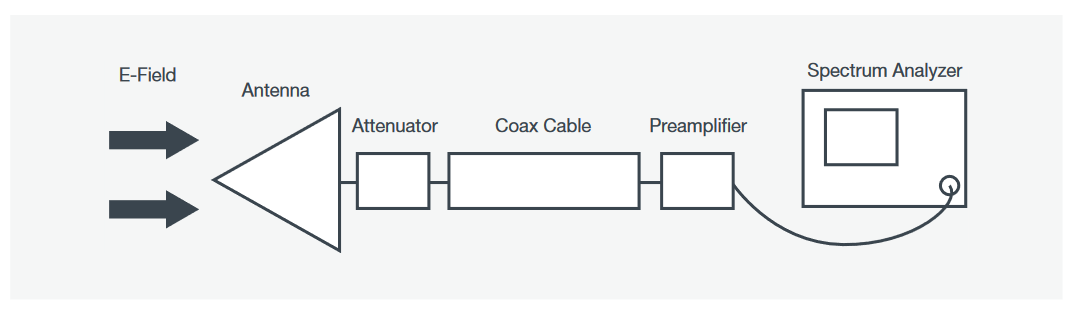
To set up a pre-compliance test for radiated emissions, it's a little more involved than for conducted emissions. You'll need to gather the following equipment. Tektronix includes all this (except the equipment table) for a special package price.
- Spectrum analyzer that covers the frequency range required. For most commercial or consumer products, you'll need to cover the range 30 MHz to 6 GHz.
- Calibrated EMI antennas that cover the ranges 30 MHz to 1 GHz (typically a wideband dipole designed for 30 to 200 MHz and a log-periodic designed for 200 to 1000 MHz) and 1 to 6 GHz (typically a horn antenna designed for 1 to 18 GHz). These will come with antenna factor calibration data.
- An insulated (non-metallic) tripod that can support the antennas at 1m height, or more.
- A broad band preamplifier (20 to 30 dB gain over the required frequency range).
- A table 80 cm high and large enough to hold the EUT and cables. Ideally, this should be rotatable (perhaps using castered wheels on the legs).
- Enough high-quality coaxial cables to connect the antennas through the preamplifier to the spectrum analyzer.
Given a calibrated EMI antenna spaced 3m or 10m away from the EUT, you can calculate the E-field (dBμV/m) by recording the dBμV reading of the spectrum analyzer and factoring in the coax loss, external preamp gain (if used), any external attenuator (if used), and antenna factor (from the antenna calibration provided by the manufacturer). See Figure 14.
This calculation can then be compared directly with the 3m or 10m radiated emissions test limits using the formula:
E-field (dBμV/m) = SpecAnalyzer (dBμV) – PreampGain (dB) +
CoaxLoss (dB) + AttenuatorLoss (dB) + AntFactor (dB)
Note that EMCVu automatically calculates the E-field using this equation assuming all the gains and losses have been entered in to the Accessories setup screen in the Setup Wizard.
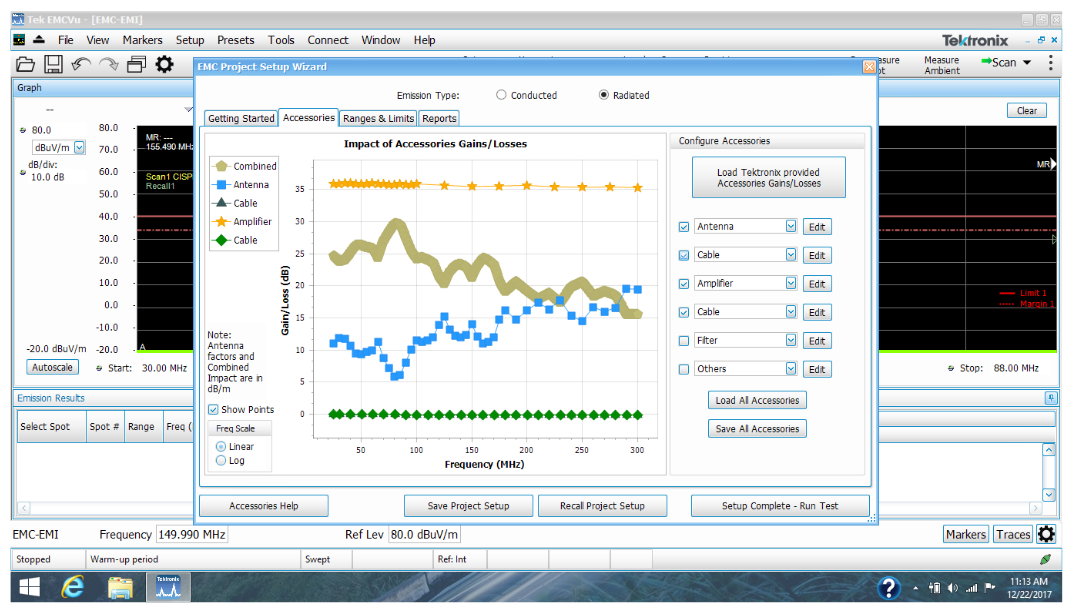
The first step when using EMCVu, is to use the Setup Wizard and add the antenna factors, coax cable loss, preamplifier gain, and any other gains or losses, such as an optional 6 dB attenuator at the antenna, in the measurement system (Figure 15). If you purchase the equipment suggested by Tektronix, these gains and losses are pre-populated when the various accessories are selected.
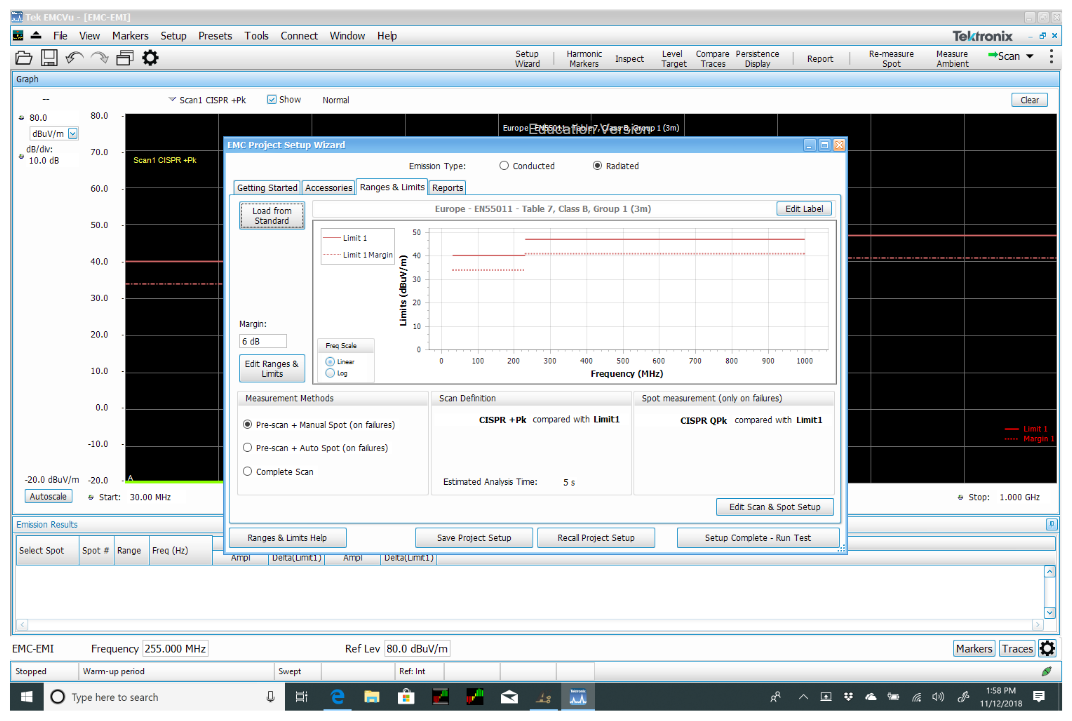
The next step will be to select the desired test limits according to the EMC standard appropriate for your product. Choices include US (FCC), Europe (EU), and Military (MIL-STD-461). Select Class A for industrial environments and Class B for consumer environments. Generally, you'll use the 3m test distance for most in-house pre-compliance testing. This is also where you'd edit the desired scan and spot (manual or automatic) setup, as well as setting the desired detector settings (such as CISPR Peak+, Average, CISPR Quasi-Peak, etc.) The default detector settings are CISPR Peak+ and CISPR Quasi-Peak, which is usually what you want to measure. See Figure 16.

Lastly, select the report generator and fill in the boilerplate information on your company, location, contact information, and equipment under test (model and serial number), etc. (Figure 17). This report generator will automatically capture test data, test descriptions, and photographs as you progress with pre-compliance testing or troubleshooting.
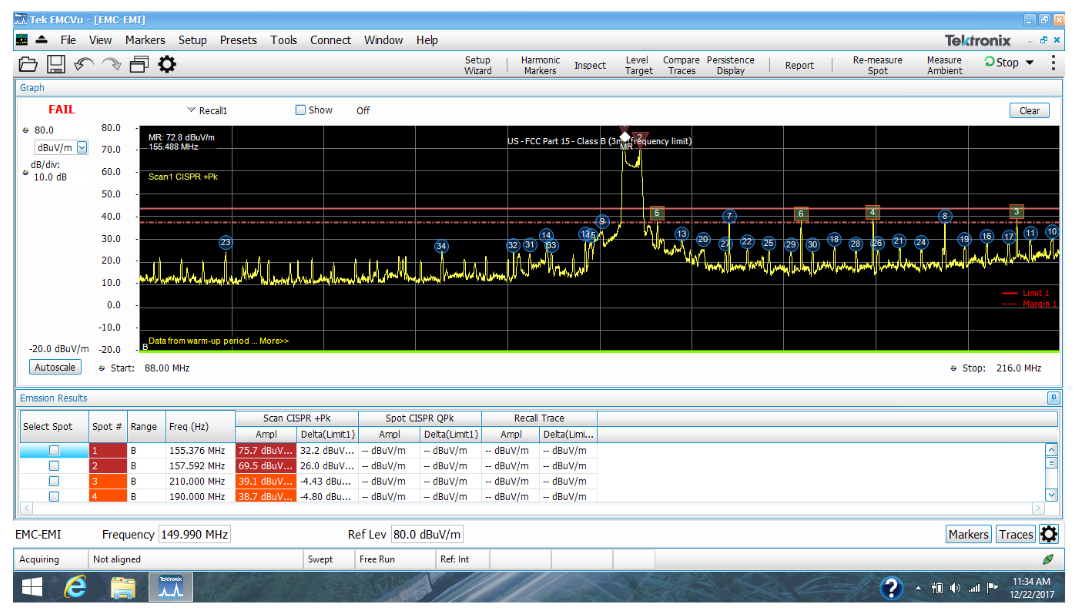
Pressing "Setup Complete – Run Test" will quickly sweep and capture all harmonic signals within the test frequency start and stop limits. It will also automatically number and sort the harmonics from highest to lowest amplitude in tabular format underneath the scan, indicating over limit (in red triangles), between the margin and the limit (in orange squares), and below the margin (in blue circles). See Figure 18.
There's really no limit to the number of harmonic signals that may be captured in one sweep. All this data can be captured in the report by clicking "Report" and adding the test set up or experiment description, adding photos, and then clicking on Save. All other data (plus time/date stamp) for that test is documented and recorded automatically. This sequence may be repeated to capture a running record of the troubleshooting experiments or pre-compliances tests desired.
Ambient Signals (see sidebar) - Before you perform a precompliance test, you'll want to record the various ambient transmitter signals (the current RF environment), first, before measuring the product under test.
To account for ambient signals using EMCVu, first make sure the screen is clear by clicking on the Clear button in the upper right corner. Then ensure the EUT is off and click on Measure Ambient in the upper right set of tabs. This will record a single sweep of the various broadcast stations, two-way radios, digital TV, and cellular phone signals. Then, turn on the EUT and click on Scan to record both the ambient and EUT signals. You'll end up with a screen similar to Figure 19.
Probable ambient signals are highlighted in blue (in the table) and violet in the scan. Product emissions are highlighted in yellow in the scan. Where the two colors overlap indicates a likely ambient.
To observe the actual product emissions more clearly, let's take the two saved traces and subtract them. This should subtract out the ambient information, leaving us with a plot of only the product emissions. To do this, click on Compare Traces in the upper tabs and the Math window will pop up at the bottom of the screen (in pink). By default, this will be "Scan1 minus Ambient" and theoretically should show harmonic spikes (spots) for actual product emissions.
You'll notice a lot of activity around the FM broadcast band (88-108 MHz), the digital TV band (470 to 608 MHz), and cellular phone (generally 600 to 850 MHz for bands below 1000 MHz). Refer to Wikipedia for more details above 1000 MHz.
Ambient Signals - One problem you'll run into immediately when testing outside of a shielded room or semi-anechoic chamber, is the number of ambient signals from sources like FM and TV broadcast transmitters, cellular telephone, and two-way radio. This is especially an issue when using current probes or external antennas. When manually using a spectrum analyzer, you'll usually want to run a baseline plot on the analyzer using "Max Hold" mode to build up a composite ambient plot. Then, activate additional traces for the actual measurements. For example, good practice is to record three plots or traces on the screen; the ambient baseline, the "before" plot, and the "after" plot with some fix applied.
Often, it's easier to narrow the frequency span on the spectrum analyzer down to "zero in" on a particular spot frequency, thus eliminating most of the ambient signals. If the harmonic is narrow band continuous wave (CW) partially hidden amongst nearby FM broadcast signals, then reducing the resolution bandwidth (RBW) can also help separate the EUT harmonics from nearby ambients. Just be sure reducing the RBW doesn't also reduce the spot amplitude as well.
Another caution is that strong nearby transmitters can affect the amplitude accuracy of the measured signals, as well as create mixing products that appear to be spot frequencies but are really combinations of the transmitter frequency and mixer circuit in the analyzer. You may need to use an external bandpass filter at the desired spot frequency to reduce the effect of the external transmitter. EMI receivers generally have these built-in preselection filters. All these techniques are described in more detail in Reference 5.
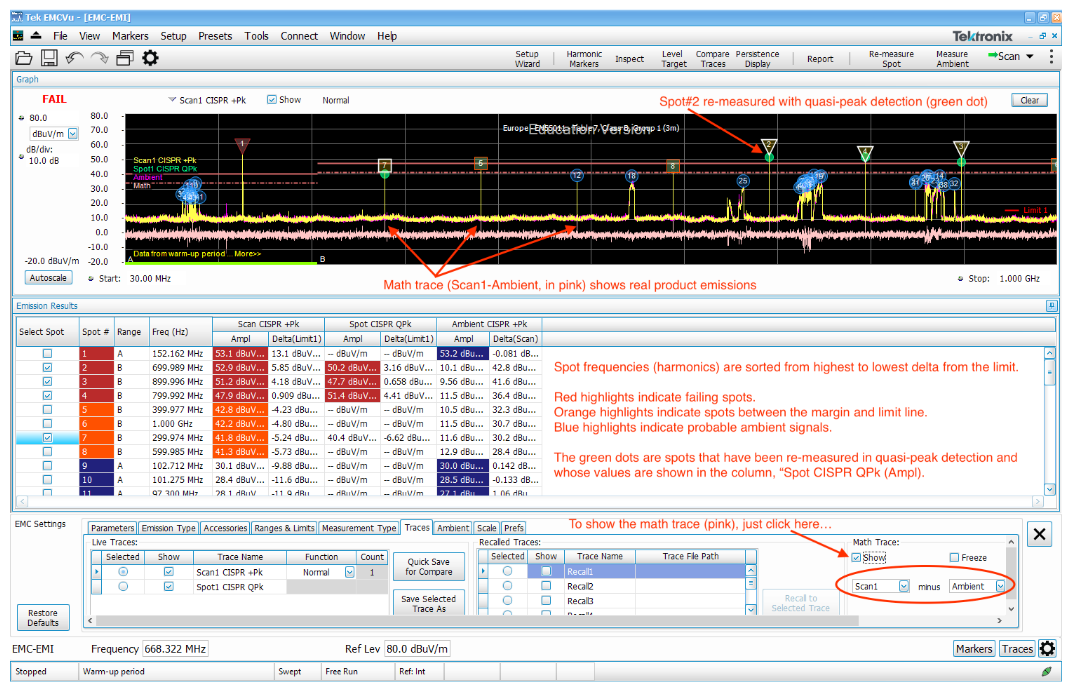
It's not foolproof, as there may be additional two-way radio transmissions that are not caught in the single Ambient sweep, but it will still give you a good idea as to what signals are coming from the product under test. To confirm whether a spot frequency is from the EUT, you may need to power it off occasionally.
Once you're in troubleshooting or pre-compliance testing mode, you can re-measure suspected EUT emissions by selecting the spot frequency in the table (or spot) and clicking on Re-measure Spot. If you've chosen to use the default detectors, this will switch to the quasi-peak measurement and record the remeasured value in the column "Spot CISPR QPk". A green dot will also be placed on the new measured value. In most cases, the remeasured quasi-peak value will be the same as the CISPR Peak+ value for continuous wave (CW) spot frequencies. If there's modulation or digital gating on the spot frequency, CISPR QPk will measure less.
PRE-COMPLIANCE TESTING FOR CONDUCTED EMISSIONS
Conducted emissions is usually not an issue given adequate power line filtering, however, many low-cost power supplies lack good filtering. Some generic "no name" power supplies have no filtering at all!
Conducted emissions testing is performed according to the international standards CISPR 11 or 32 and requires a line impedance stabilization network (LISN) between the source of AC line (or DC) voltage and the product under test. A spectrum analyzer is connected to the 50-Ohm port and the conducted RF noise voltage is displayed on the analyzer. Different model LISNs are made for either AC or DC supply voltage. Tektronix offers an affordable LISN with built-in transient protection.
Ideally, you'll set up the test according to the CISPR 11/32 standard as illustrated in Figure 20. The equipment under test (EUT) is placed on a wooden table 80 cm high with a ground plane at floor level. The LISN is bonded to the ground plane and connected to the EUT and spectrum analyzer.
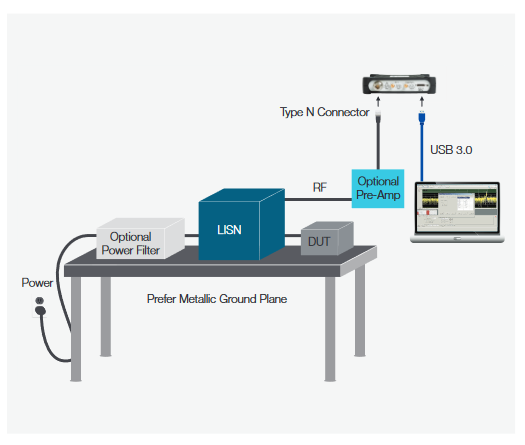
Testing for conducted emissions will be described in this application note with less detail, because the process is essentially the same as for the radiated emissions test. Using the Setup Wizard in EMCVu, you'll select Conducted Emissions and choose the appropriate standards and limits. The rest of the measurement and troubleshooting process is the same.
Obtain a Line Impedance Stabilization Network (LISN) and position it between the product or system under test and the spectrum analyzer. Note the sequence of connection below!
CAUTION: It's often important to power up the EUT prior to connecting the LISN to the analyzer. This is because large transients can occur at power-up and may potentially destroy the sensitive input preamplifier stage of the analyzer. Note that the TekBox LISN has built-in transient protection. Not all do…you've been warned!
Power up the EUT and then connect the 50-Ohm output port of the LISN to the analyzer. Note the spot frequencies are usually very high at the lower frequencies and taper off towards 30 MHz. Be sure these higher spot frequencies don't overdrive the analyzer. Add additional input attenuation, if required. The LISN supplied by Tektronix has a 10 dB attenuator when the transient suppressor is switch in.
By comparing the average detected peaks with the appropriate CISPR limits, you'll be able to tell whether the EUT is passing or failing prior to formal compliance testing. Troubleshooting spot frequencies is similar to the radiated emissions testing described previously
Summary
By developing your own EMI troubleshooting and precompliance test lab for radiated and conducted emissions, you'll save time and money by moving the troubleshooting process in-house. This will save you time and cost when compared to depending on commercial test labs for initial testing.
Most of the high-risk EMI tests are easily performed with low-cost equipment. The cost savings by performing troubleshooting at you own facility can mount up to hundreds of thousands of dollars and weeks or months of product delays.
As technology continues to advance, we EMC engineers and product designers need to upgrade our usual analysis and pre-compliance test tools to stay one step ahead and be able to better capture and display the more unusual emissions expected. Real-time spectrum analyzers have already proven to be invaluable for EMI debug and troubleshooting. Advanced spectral analysis will be especially important as mobile devices continue to shrink and more products incorporate wireless and other advanced digital modes.